The most compact, flexible and reliable tube header.
Hotline : +41 840 84 84 84
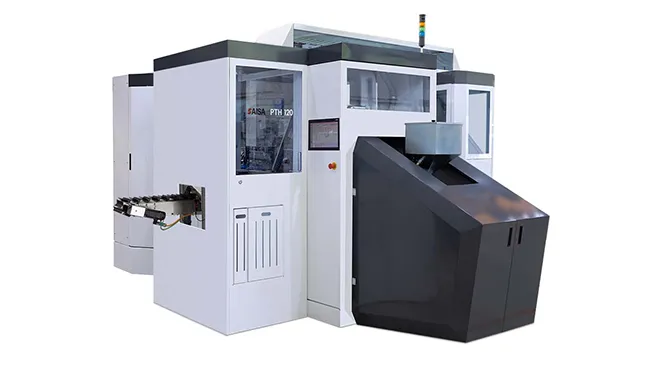
■ Key benefits
- Robust, reliable machine for minimised production costs
- Ultra-compact with easy access
- User-friendly interface
- Great flexibility to meet countless tube design needs for today and tomorrow
- Flexible line integration solution to suit multiple configurations
- Compatibility with existing standard Synchroflow™ tooling
The PTH 120 heading machine enables the heading of tubes at speeds of up to 120 pieces per minute. It covers diameters ranging from 13.5 mm to 60 mm. An output of 120 tubes per minute is guaranteed even when producing large tubes of Ø60 mm with a 1.2 mm shoulder thickness.
But what is “tube heading”? The tube heading process consists of forming a shoulder and simultaneously bonding it to the tube body.
Thanks to Aisa well-proven Synchroflow™ 2-step compression moulding technology, tubes achieve excellent aesthetics and a perfect welding of the shoulder. Moreover, this high-quality system enables great freedom and flexibility in master batch colour choice, as well as the use of recyclable and recycled materials. Less than 10 minutes is enough to change tube decoration or tube length.
With the new thickness control option, dosing can be now self-regulated for constant shoulder thickness.
Very easy to integrate in a production line, the PTH 120 can be installed in many line configurations:
- Linked to upstream machines such as the Aisa BM 120 body maker or DXL 120 sleeve maker, or with a third-party printer/extruder by way of a pin-chain conveyor.
- Linked downstream to Aisa CM 120 capping machine through direct transfer or accumulator.
- …and more!
Choose Aisa PTH heading machines for a reliable equipment that adapts to your changing needs and evolves with packaging trends.
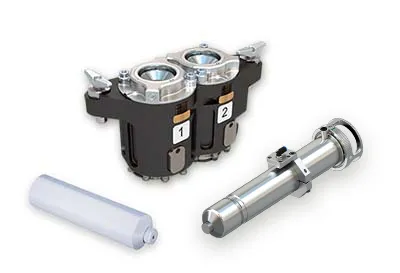
High-cooling tooling
Designed for optimal cooling efficiency and increased machine performance
- Reduced tooling weight.
- Optimised cooling circuit for better heat exchange.
- Up to 20% higher productivity compared to standard Synchroflow™ tooling.
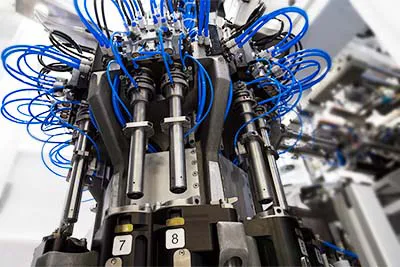
Thanks to a radically new design, the main turret of the PTH 120 machine reduces weight, indexing time, and maintenance costs.
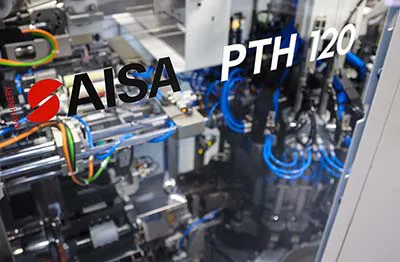
The sleeve transfer system is designed to handle tube sleeves from an (optional) up-stream accumulator via pin-chain, in a positive and always controlled way.
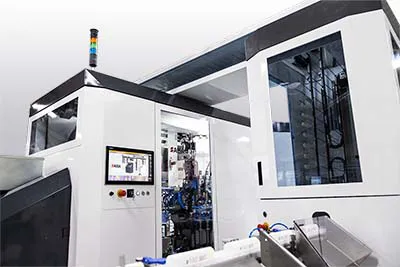
Pin-chain infeed conveyor offers simple transfer from an upstream machine.
Technologies :
(Click on the icon for more information)
Machine specifications
Machine capabilities
Up to 120 tubes/min.
Tube Ø13.5 mm to 63.5 mm
Tube length 50 mm to 230 mm
Value-adding options
Printed sleeve orientation
Oval tube heading system
Accumulators for line integration
Live machine checks and service via internet
Quality Control Systems
Shoulder thickness measurement
Shoulder and orifice quality control
Sleeve orientation inspection
Closed-loop thickness regulation
Overall dimensions
Length ~4.68 m [~15ft] (including pin-chain infeed conveyor)
Width 5.15 m [16 ft]
Height 2.7 m [8.8 ft]