Multilayer barrier compression moulding
■ What is it?
Bacomex™ is a multilayer barrier moulding technology. In the production of laminate and extruded tubes, the moulded shoulder has a reputation for being the weakest part, where oxygen can enter and aromas and vitamins escape.
Bacomex™ multilayer compression moulding technology is an efficient barrier protection embedded into the entire tube head.
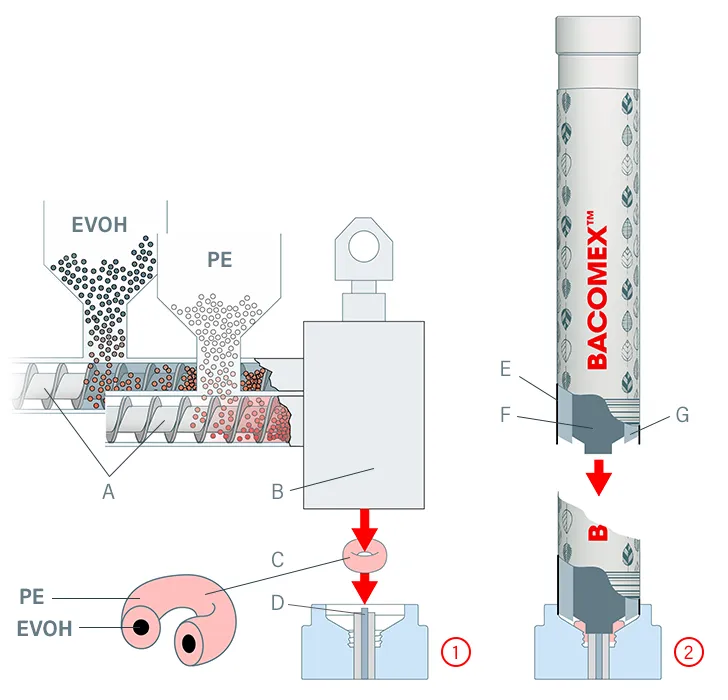
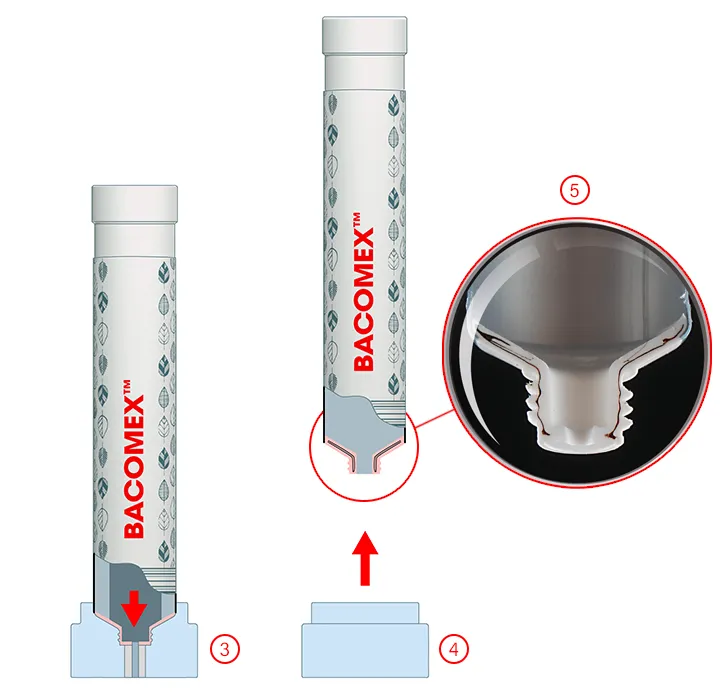
1. A controlled flow under pressure traps the EVOH barrier in the middle of the PE doughnut.
2. Outer and inner parts (F)(G) of the mandrel are pushed down. The outer part (G) of the mandrel closes the mould before pressure is applied.
3. Inner part (F) of the mandrel is pushed further down to form the mould for the tube head.
4. The mandrel lifts up; the shoulder is perfectly moulded and welded with a clean orifice to the sleeve. The multilayer barrier is formed during the compression moulding.
5. Shoulder performance
— Good EVOH layer distribution
— Shoulder and neck covered
— Oxygen permeability < 0,0012cc/pack/24h
— Barrier improvement factor = 3 to 6
A. Two extruders with axial pressure piston
B. Dosing system
C. Doughnut (PE/EVOH/PE dose)
D. Orifice pin
E. Sleeve
F. Internal mandrel
G. External mandrel
■ Available on
PTH 90, PTH 150 and SFM 100 machines running at outputs of 90, 147 tubes/min. and 100 shoulders/min.
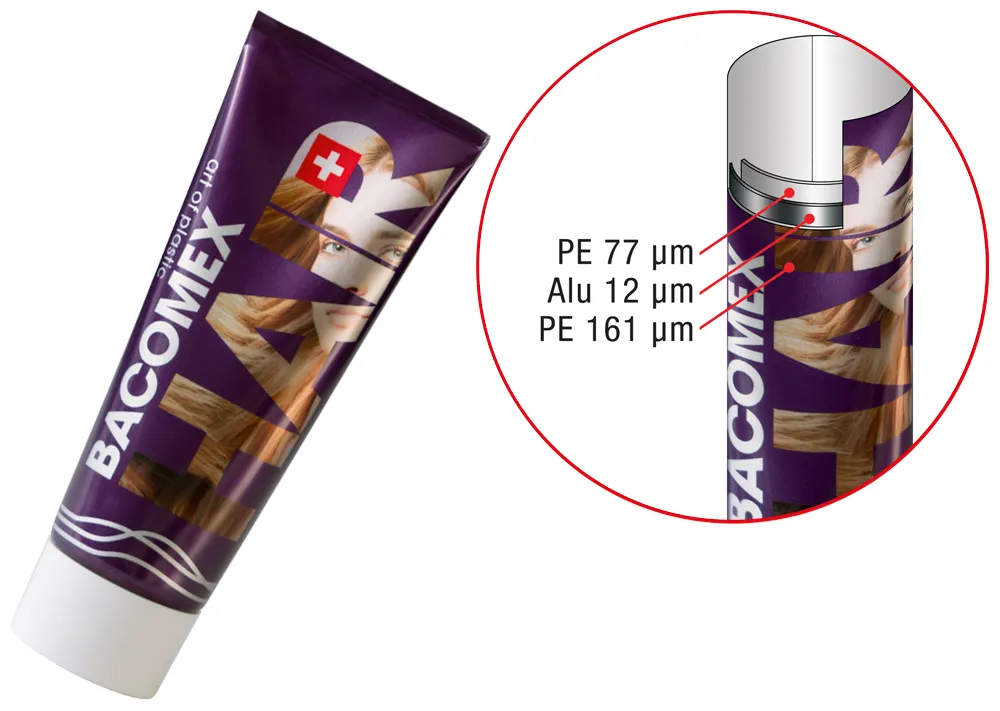
Hair
■ Packaging technology
- Symmetric PE laminate sleeve structure; 250 µm thick with 12 µm aluminium barrier layer.
- Induction welded overlap seam.
- Bacomex™ shoulder, PE with layers of EVOH barrier material.
- Cylindrical screw-on cap.
- Improved barrier properties vs standard ABL tube (BIF 12.5).
- Bounce-back index: 47%.
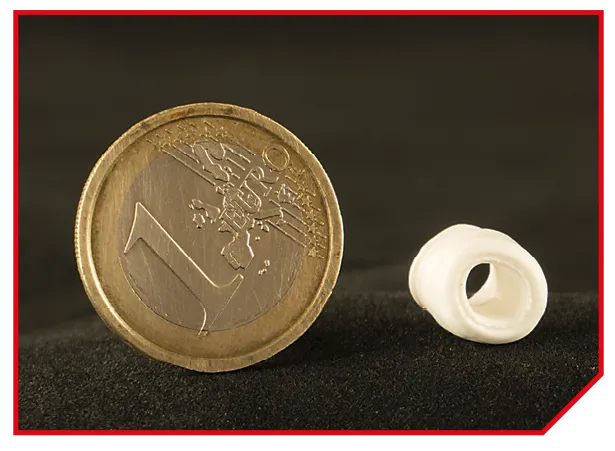
■ Technical achievement
- Very low dosing weight.
- 25 mg EVOH barrier resin.
- 475 mg PE resin.
- Precise layer distribution.
- Reproducible dosing process and shape.
High barrier solutions
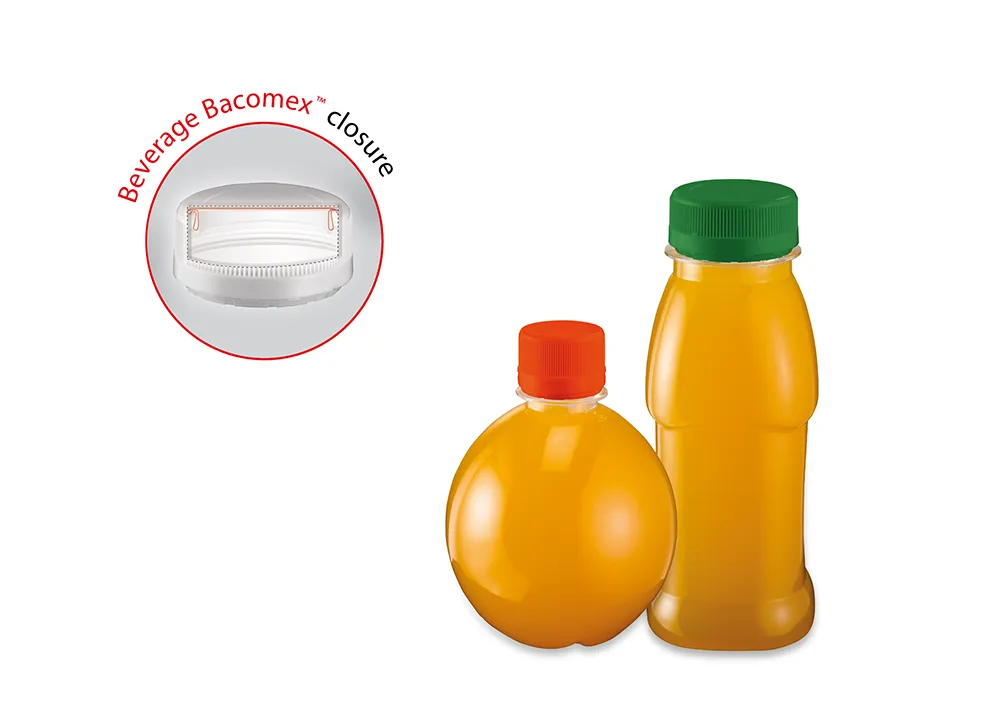
■ What is it?
Bacomex™ is a high-tech barrier production process, that is both efficient and cost effective. This plastic, multilayer compression moulding solution has been developed by Aisa for multiple plastic packaging applications.■ Results
- Oxygen barrier improvement factor (BIF) between 6 and 18.
- Flavour barrier improvement factor (BIF) of 100 and higher.
■ How does it work?
- With the Bacomex™ process, a two-layer extruded dose is placed into the mould, and the compression mandrel forces the two materials towards the outer edge of the cavity to form a 5-layer structure made up of two EVOH layers and three PE or PP layers. The result is a high barrier integrated into the moulded component.
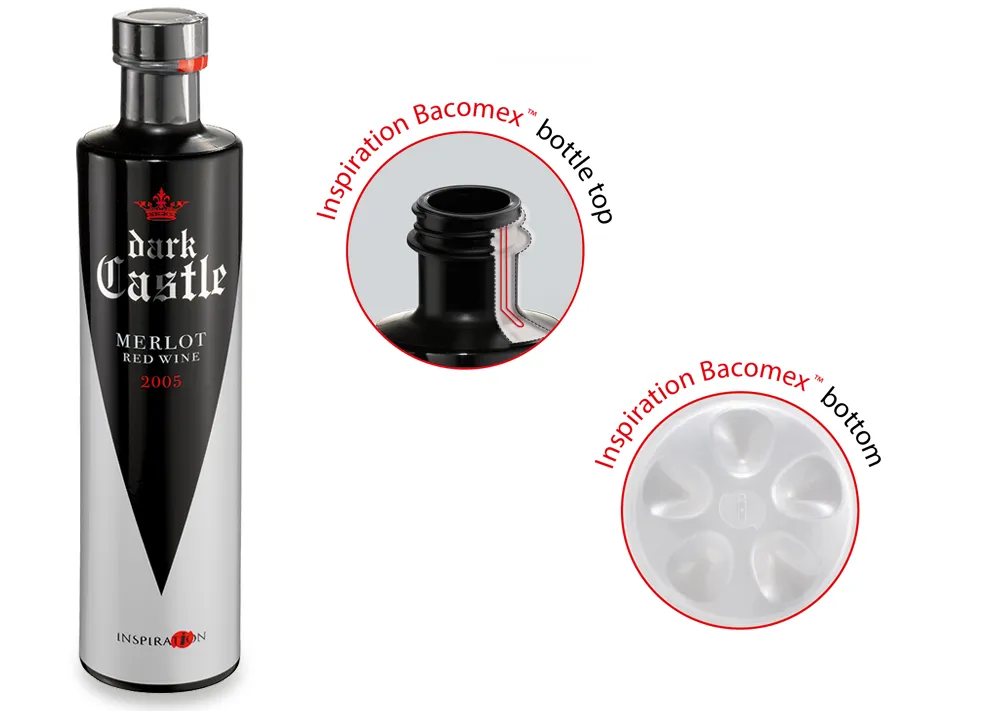
■ Packaging performance
- Inspiration 375 ml bottle with Bacomex™ barrier components:
1.75 ccO2/pack/year/atm. - Bacomex™ bottle cap 38 mm BIF=4 or 0.0056 ccO2/pack/day/atm.
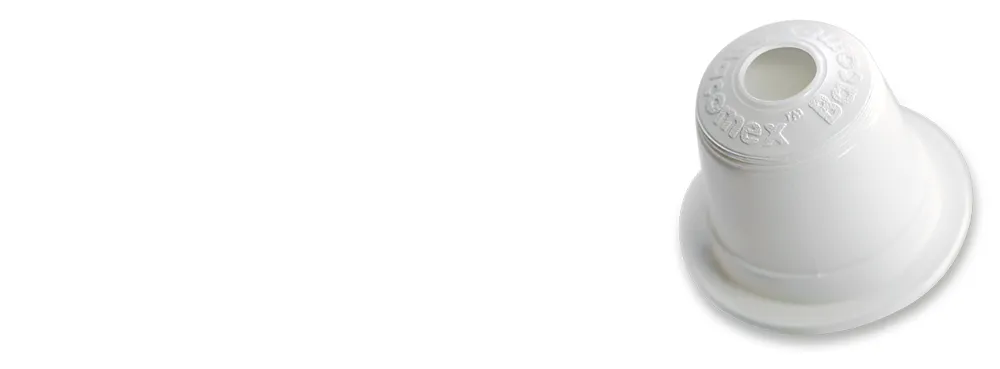
■ |
Bacomex™ barrier coffee capsules with or without a hole at the top. |
Our other technologies :
Do you have a question?
Contact us now for more information!